Pipe mixer
Static and dynamic pipe mixer development
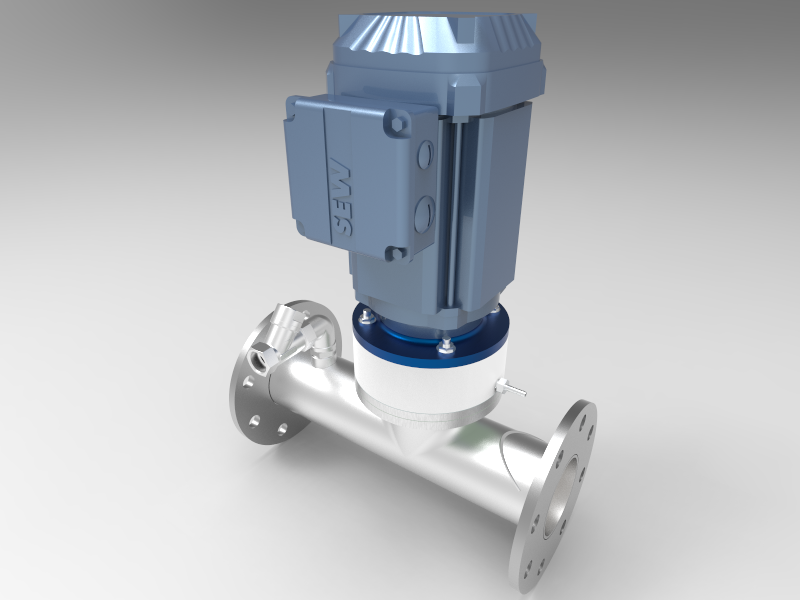
In 2022, together with colleagues from AMCON Europe s.r.o., we developed and tested prototypes of a pipe mixer in two versions: static and dynamic. In 2023, the product was successfully launched.
Development
The pipe mixer is a device that enables the mixing of chemicals without the need for tanks. This solution is commonly used in the dosing of flocculant/coagulant into wastewater sludge before dewatering. AMCON Europe s.r.o. specializes in providing tailored thickening and dewatering services to European wastewater treatment plants. Last year, we had the pleasure of collaborating with this company on a project to optimize chemical dosing during dewatering. One of the outcomes of this project is the pipe mixer (also known as a mixer).
The principle of the device is simple. A special mixing insert inside the pipe promotes transverse flow, which induces the mixing of liquids.
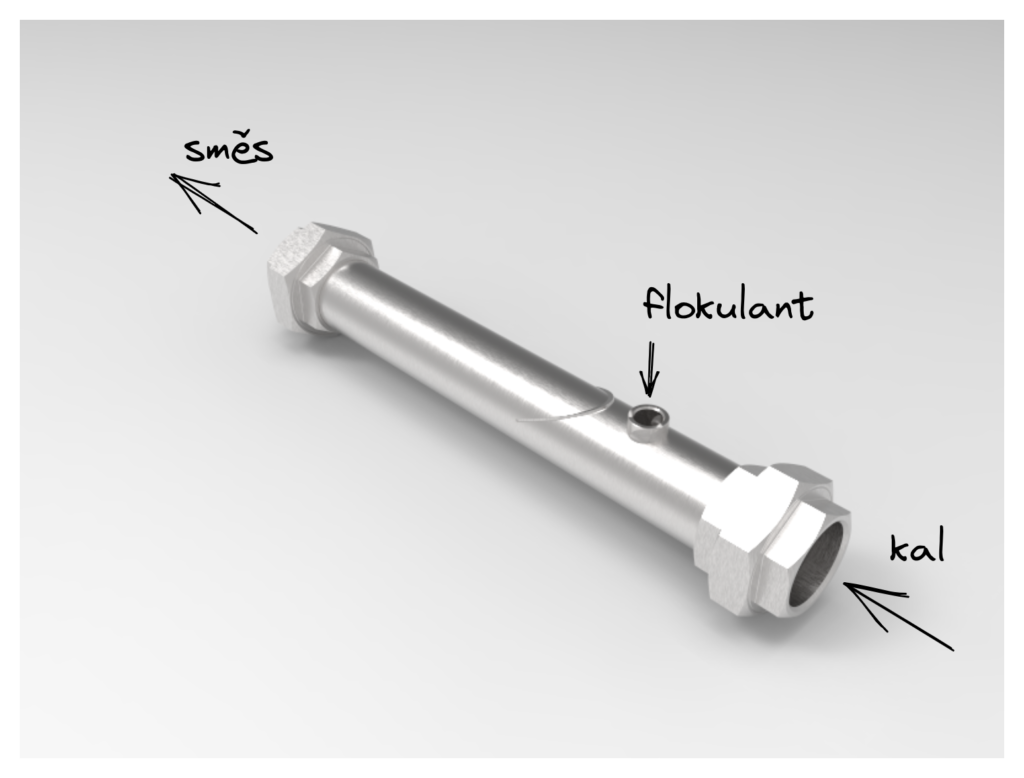
In the case of the dynamic mixer, mixing occurs with the help of a mixer mounted on the motor shaft (as shown in the introductory image of the article). While the principle is quite simple, optimizing the mixing elements is not. After all, the goal of developing our own device is to ensure that:
- The mixing efficiency is greater than that of competitors
- The pressure loss and manufacturing cost are lower.
This is where our work begins. By combining CFD simulations with machine optimization, we achieved unexpectedly good results. We generated dozens of designs with different placements of the mixing elements and various blade shapes. In the graph below, you can see them plotted according to pressure loss and mixing efficiency.
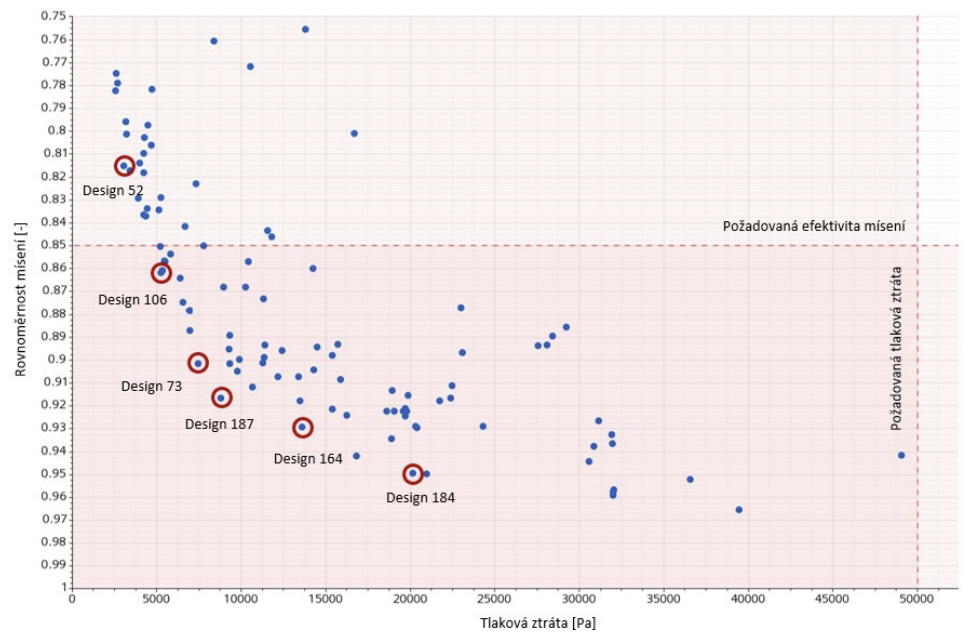
We then optimized the shape and placement of the mixing elements based solely on manufacturability. This resulted in the first prototype.
Validation
These mixers have been successfully validated in practice several times, namely at a wastewater treatment plant (WWTP) near Prague. However, it is well-known that every model needs to be validated as well. Validation serves as proof that we can continue to rely on our CFD models. We opted for testing the prototypes on a specially built test rig in the water management hall at the Faculty of Civil Engineering, CTU in Prague.
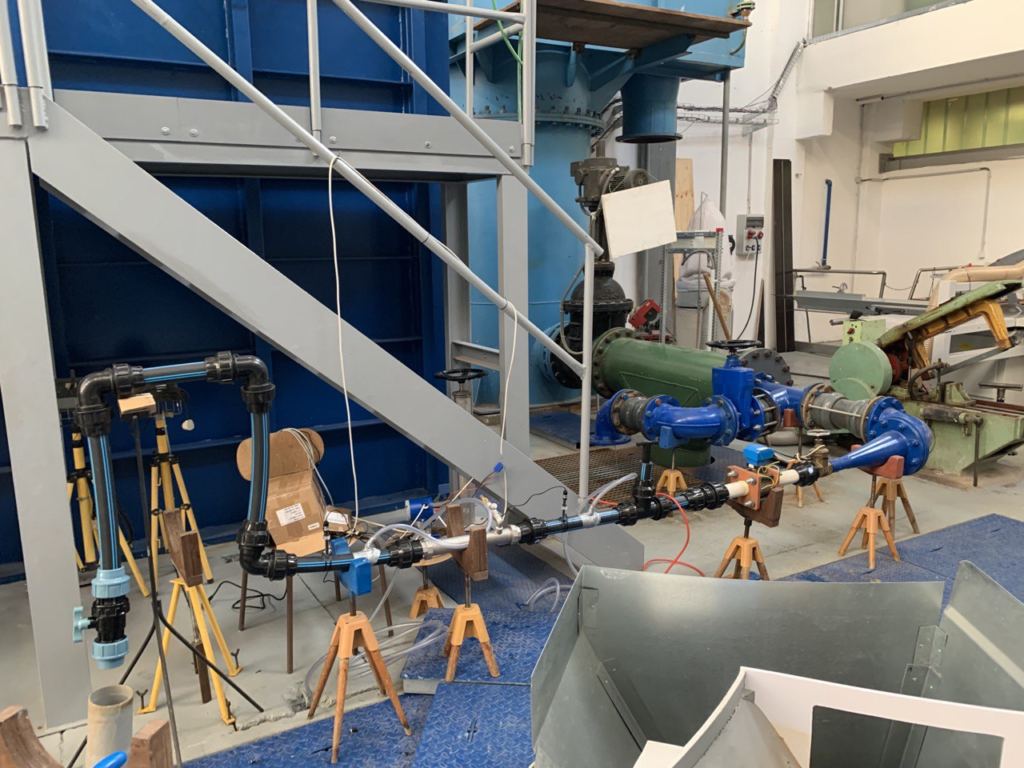
For the purpose of evaluating the mixing process, we chose to monitor conductivity fluctuations before and after the mixer. During the flow, we dosed a saline solution into the mixer, which has a much higher conductivity than the incoming water. The conductivity sensor after the mixer was designed to capture these fluctuations in conductivity. When the variability is negligible, it indicates effective and stable mixing. Conversely, if variability is significant, the mixing can be considered insufficient and unreliable. Fortunately, our prototype showed low variability, meaning we can consider our CFD model successfully verified through this direct method.
These two mixers were not the only outputs from this project. The next steps involved optimizing the flotation unit and developing equipment for evaluating the dewaterability of wastewater sludge. We’d be happy to assist you with similar projects in the field of sludge dewatering or chemical mixing.